
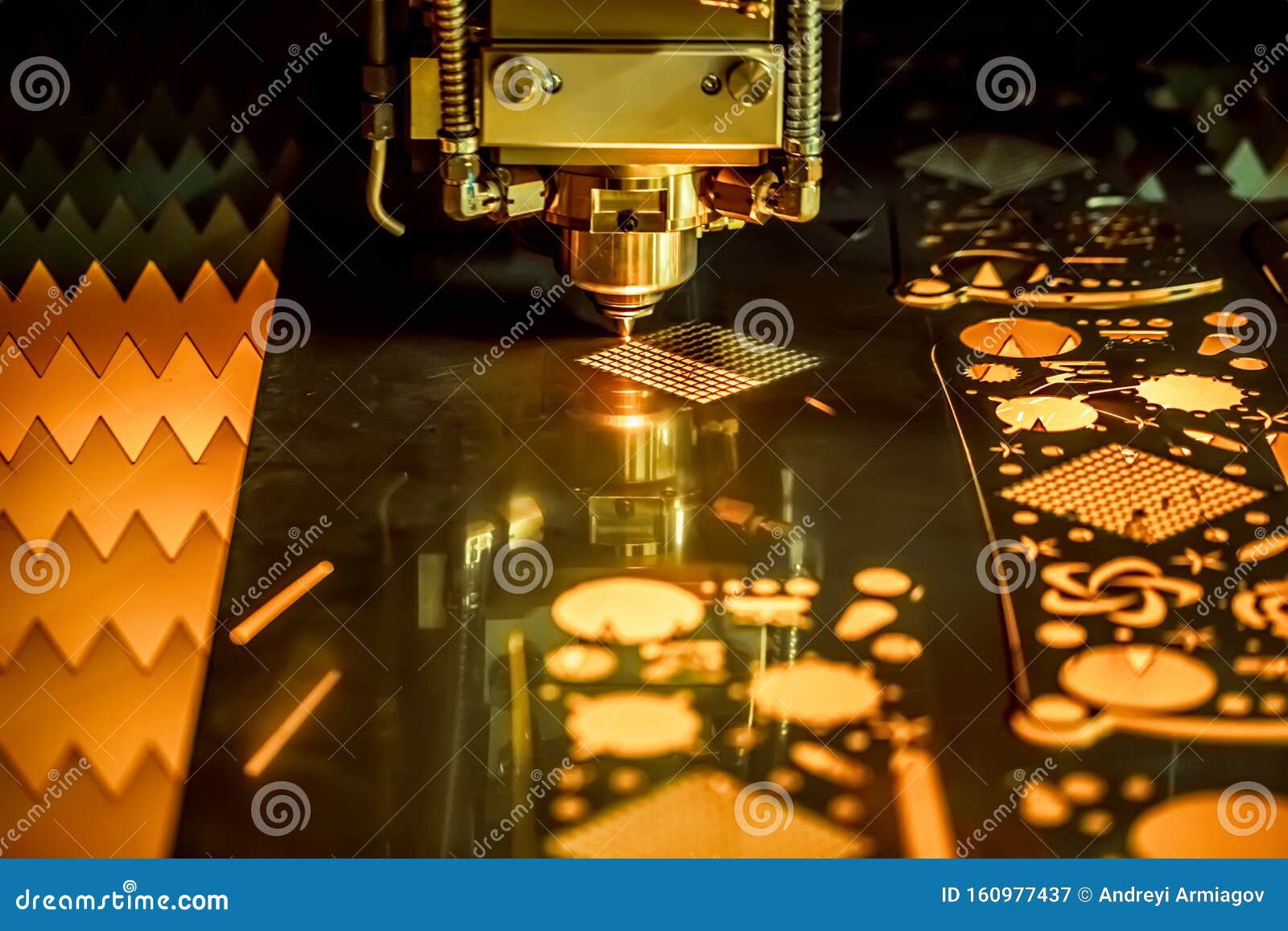
For sheet metal cutting, the focal length is usually 1.5–3 inches (38–76 mm). In order to achieve the smoothest possible finish during contour cutting, the direction of beam polarization must be rotated as it goes around the periphery of a contoured workpiece. This beam is normally focused and intensified by a lens or a mirror to a very small spot of about 0.001 inches (0.025 mm) to create a very intense laser beam. The parallel rays of coherent light from the laser source often fall in the range between 0.06–0.08 inches (1.5–2.0 mm) in diameter. Piercing usually involves a high-power pulsed laser beam which slowly makes a hole in the material, taking around 5–15 seconds for 0.5-inch-thick (13 mm) stainless steel, for example. In order to be able to start cutting from somewhere other than the edge, a pierce is done before every cut. Depending upon material thickness, kerf widths as small as 0.004 inches (0.10 mm) are possible. The narrowest part of the focused beam is generally less than 0.0125 inches (0.32 mm) in diameter. The quality of the beam has a direct impact on the focused spot size. The laser beam is generally focused using a high-quality lens on the work zone.
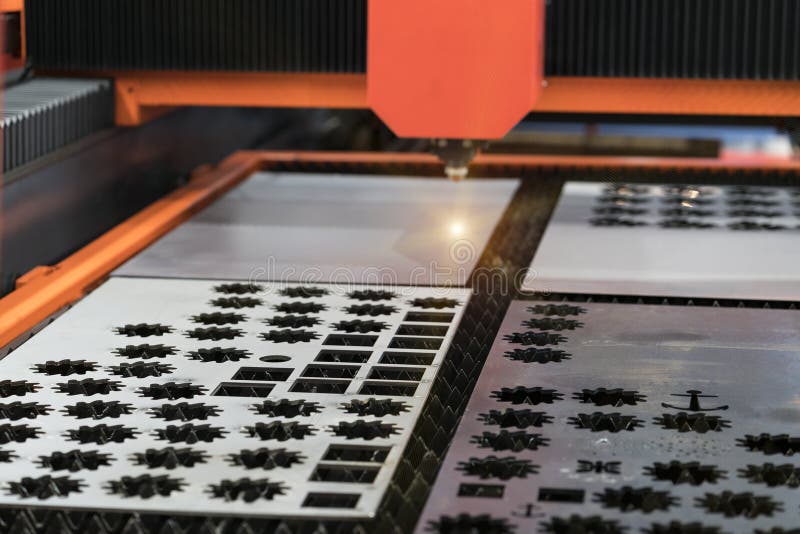
Industrial laser cutting of steel with cutting instructions programmed through the CNC interface

At the same time CO 2 lasers were adapted to cut non-metals, such as textiles, because, at the time, CO 2 lasers were not powerful enough to overcome the thermal conductivity of metals. In the early 1970s, this technology was put into production to cut titanium for aerospace applications. In 1967, the British pioneered laser-assisted oxygen jet cutting for metals. This machine was made by the Western Electric Engineering Research Center. In 1965, the first production laser cutting machine was used to drill holes in diamond dies.

The focused laser beam is directed at the material, which then either melts, burns, vaporizes away, or is blown away by a jet of gas, leaving an edge with a high-quality surface finish. A commercial laser for cutting materials uses a motion control system to follow a CNC or G-code of the pattern to be cut onto the material. The laser optics and CNC (computer numerical control) is used to direct the laser beam to the material. Laser cutting works by directing the output of a high-power laser most commonly through optics. While typically used for industrial manufacturing applications, it is now used by schools, small businesses, architecture, and hobbyists. Laser cutting is a technology that uses a laser to vaporize materials, resulting in a cut edge. CAD (top) and stainless steel laser-cut part (bottom)
